ON-LINE
MANUAL
General Information
General information
on pneumatic external vibrators
Introduction
This manual contains information on the two main types of vibrators:
• Rotary vibratord (ball,
roller and turbine vibrators)
• Linear piston vibrators
Historical Background...
Even today in some areas of the globe, just as it was centuries
ago, the hand driven stamper still is very common as a tool to
compact concrete in molds. Similarly, the sledge hammer is the
tool used to support the material flow.
Screens to separate chaff from
corn are known to be the first vibrating application "industrialized",
i.e. the first vibrating element driven by non-human energies
such as water and wind.
Pneumatic driven vibrators were
introduced early this century as linear piston vibrators or pneumatic
hammers. Only years later was the simpler rotary vibrator with
a ball or a roller running circle born. For decades this design
has not been changed. The body was and still is made by many
manufacturers of cast iron and the outside surface is not machined.
At the end of the sixties, the
first experiments with aluminum bodies were conducted. Aluminum
is very simple and clean to machine, with no black casting dust
that covers machines and the hands of the end users. Aluminum
has the strength required but is not too stiff to allow cracks
to form. It can be coated with paint so that modern industrial
designs can be created. For applications in special environments
such as pharmaceutical installations bodies are machined from
stainless steel.
Today, a vast amount of work
is done by vibrators. The main applications are emptying bins
and hoppers, screening materials, and compacting concrete as
well as feeding sand, clay, or any kind of powder or small parts
such as screws. Vibration is also used in the electronics industry
to detect cold joints on printed circuit boards.
In silo and bin applications
air blasters are used to loosen bulky materials. Most of our
agents and representatives sell air blasters as well as vibrators
since the products complement each other.
Classification of vibrators
Vibrators can be classified in general according to the type
of energy they use and the vibration technology :
ENERGY TYPE |
TECHNOLOGY |
Electric
Pneumatic
Hydraulic
|
Rotary/Linear/Magnetic
Rotary / Linear
Rotary |
Basic Information On
Pneumatically Driven Vibrators
What is a vibrator good for?
As previously stated, with the
help of vibration any kind of bulky material can be fed, compacted
or separated. In most cases vibration supports the force of gravity.
For instance, bulky material may "hang" and clog in
a hopper because of moisture. Vibration can loosen the material
so the force of gravity can continue to move material through
the hopper.
Another application for vibrators
is their use with concrete. Vibrating concrete means to shake
the sand and gravel particles so that they find the most compact
volume possible, with no space available for air. Gravity is
responsible for the first line in compacting but the vibration
supports and improves it very much.
In both the cases vibration
will reduce friction of the material.
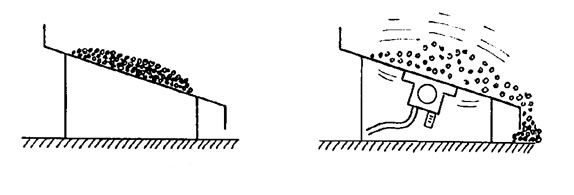
Vibrating
and gravity
Bridging
and ratholing
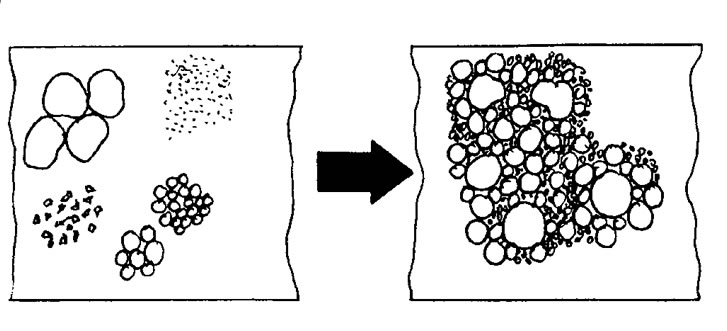
Compacting
of concrete
Vibration does not necessarily
suppor the force of gravity. Vibration makes material "jump"
and gravity brings it back to the channel or chute. With the
help of linear vibrators the direction of the material jump can
be defined, and by adjusting the amplitude the length of the
jump can be varied. When the chute slopes downward, rotary vibrators
can be used as well.
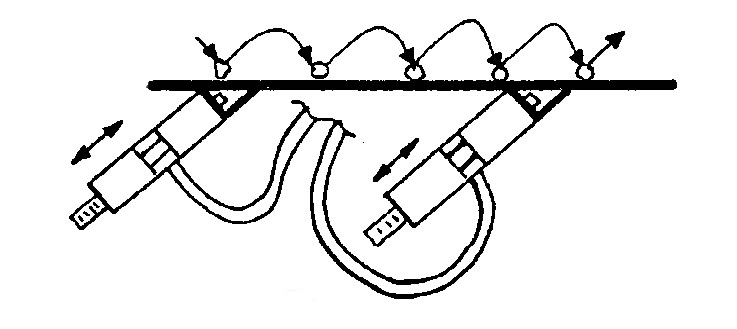
Feeding
of materials
Basic information
One thing is most important to know when dealing with any kind
of vibrators: You can certainly calculate natural frequencies
of materials, silos, chutes, etc., but in reality your results
will never be exactly as calculated.
There are tables and even calculation
schemes available to correctly select and position vibrators
with respect to a wide range of force and frequency. However,
the "fine tuning", that is, the optimal adjustment
of the vibrator, is a matter
of practical trials and tests. Field
engineers with some experience may immediately select the best
type of vibrator
as well as the optimal mounting site.
There are some rules of thumb
and tables given under "Selection of the Optimal Vibrator
Type".
To be able to perform optimal
tuning of the vibrator, it is recommended that you put an air
line regulator or a needle valve
in the air pressure line so
the air flow and the air pressure can be controlled.
Finding the natural frequency
of the material that is to be fed, compacted or separated is
the best way
to tune or adjust the vibrator.
The operational frequency range
of pneumatic external vibrators is from 2,000 r.p.m. up to about
20,000 r.p.m.
or about 35 to 350 Hz. The values given in the
technical data sheet were obtained when the vibrator is mounted
to a heavy lab test block, when the vibrator is not actually
working, that is, the amplitude is zero,
but the frequeny speeds
2 to 3 times higher than when mounted to an object.
Often the natural frequency of
the material is out of the operational frequency range of a vibrator.
Thus, a more powerful vibrator has to be used to do the job.
It is not necessary for the vibrator
to run at full power to perform at its best.
It is recommended
that you operate a new vibrator at ? of its maximum power
so that
if power is lost over time
due to abrasion, aging, etc.,
the frequency can be increased to compensate properly.
NOTE:
The pneumatic rotary and
linear vibrator must not be operated with more than 100 PSI (7 BARS) of operating pressure.
NEXT TO VIBRATOR SELECTION